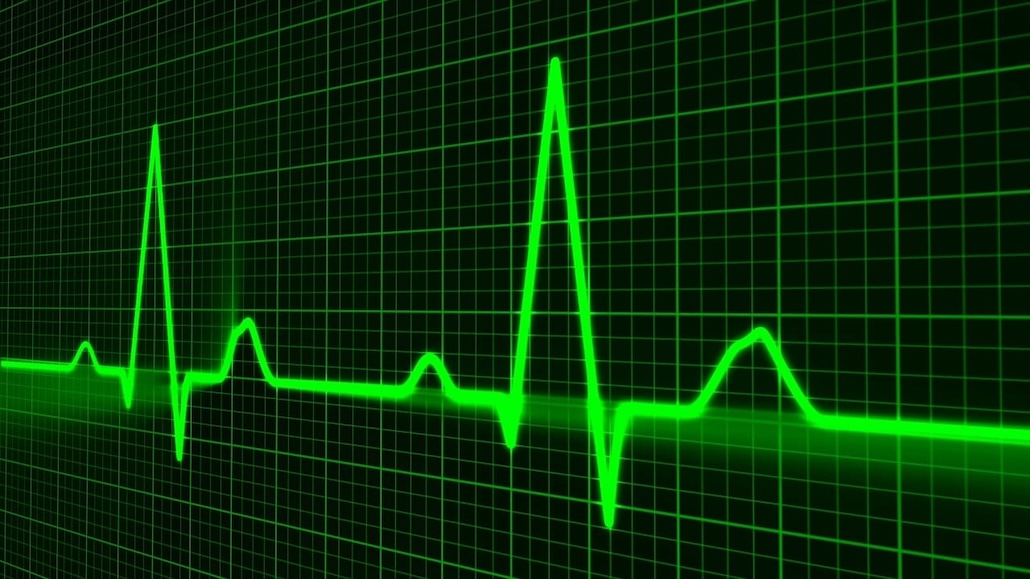
15 Mai Für die Aufgabe qualifiziert? Ein Einblick in die Gerätequalifizierung
In der Pharmaindustrie ist die Qualitätssicherung ein Schlüsselfaktor, um die Sicherheit und Wirksamkeit von Arzneimitteln und somit die Patientensicherheit zu gewährleisten. Qualitätssicherung spielt dabei nicht nur bei Wirkstoffen und Rezepturen eine Rolle, sondern erstreckt sich auch auf die Anlagen- und Gerätequalifizierung, die sicherstellt, dass eingesetzte Systeme den gesetzlichen Anforderungen entsprechen und für ihren vorgesehenen Zweck geeignet sind.
In diesem Artikel gebe ich einen Überblick über einzelne Aspekte der Gerätequalifizierung, von den erforderlichen Qualifizierungsdokumenten bis hin zu den Schritten, die Unternehmen umsetzen müssen, um Compliance und Effektivität ihrer Systeme sicherzustellen.
Gerätequalifizierung was ist das?
Gerätequalifizierung bezeichnet den Prozess, der sicherstellt, dass ein bestimmtes Gerät oder eine Anlage zuverlässig und konsistent innerhalb seiner spezifizierten Anforderungen funktioniert.
Der EudraLex Volume 4, Annex 15 befasst sich mit der Qualifizierung und Validierung und bietet Leitlinien für die Pharmaindustrie zur Sicherstellung der Qualität von Arzneimitteln.
Warum ist die Gerätequalifizierung so wichtig?
- Regulatorische Anforderungen:
Branchen wie die Pharmaindustrie unterliegen strengen, regulatorischen Anforderungen. Die Einhaltung dieser Anforderungen ist für die Erfüllung von Qualitätsstandards und die Zulassung von Produkten unerlässlich. - Risikominimierung:
Durch eine sorgfältig durchgeführte Qualifizierung von Geräten können potenzielle Risiken im Zusammenhang mit Produktionsprozessen und Qualitätsprüfungen minimiert werden. Dies trägt dazu bei, die Integrität von Prozessen und die Sicherheit von Produkten für den Patienten zu gewährleisten. - Kosteneffizienz:
Eine sorgfältig durchgeführte Gerätequalifizierung spart langfristig Kosten, indem sie die Fehleranfälligkeit der Systeme verringert, Ausfallzeiten reduziert und die Produktqualität steigert. Auf diese Weise könne teure Nachbesserungen vermieden werden.
Die einzelnen Schritte zu einer erfolgreichen Gerätequalifizierung:
Die Qualifizierung umfasst mehrere Schritte, die sorgfältig geplant, durchgeführt und dokumentiert werden müssen. Sie sollten nacheinander erfolgen und gelten in der Regel erst dann als abgeschlossen, wenn ihre Prüfergebnisse innerhalb der spezifizierten Akzeptanzkriterien liegen und die Beseitigung von Mängeln nachvollziehbar beschrieben ist.
Achten Sie bei der Dokumentation darauf, dass jeder Ihrer Schritte auch nach 10 Jahren noch von einem Laien nachvollzogen werden kann. Wählen Sie ihre Sprache möglichst frei von Fachwörtern und beschreiben sie mögliche Abweichungen vom Qualifizierungsplan besser mit ein paar Worten zu viel als zu wenig!
Qualifizierungsmasterplan [QMP]: Je nach Komplexität des Projekts kann ein Qualifizierungsmasterplan erstellt werden, der mindestens folgende Punkte beinhalten sollte:
- den Umfang und die Abfolge der Qualifizierungstätigkeiten
- die Verantwortlichkeiten
- einen Zeitplan
- die zu erstellenden und zu aktualisierenden Dokumente
- eine Liste der mitgeltenden Dokumente.
Dokumentenliste (Beispiel, ohne Anspruch auf Vollständigkeit)
Initiale Risikoanalyse: Vor dem Beginn eines Projektes sollte eine initiale Risikoanalyse durchgeführt werden, um Risiken z.B. in Bezug auf eine Neuanschaffung, systematisch zu bewerten und potenziell notwendige Maßnahmen zu identifizieren. Einige dieser Maßnahmen müssen gegebenenfalls schon in den Nutzeranforderungen berücksichtigt werden, daher ist es notwendig die initiale Risikoanalyse frühzeitig durchzuführen.
Nutzeranforderungen [URS] / User Requirement Specification: In diesem Dokument legt das Unternehmen die notwendigen Anforderungen an das System fest, damit es für den bestimmungsgemäßen Gebrauch geeignet ist. Die URS fungiert auch als Lastenheft für die Gerätehersteller und stellt die Grundlage für die zu erstellenden Qualifizierungsdokumente dar.
Funktionale Risikoanalyse [FRA]: Basierend auf den Nutzeranforderungen wird von qualifiziertem Personal eine Funktionale Risikoanalyse aller kritischen Anforderungen durchgeführt, um potenzielle Risiken und geeignete Maßnahmen zur Risikominderung zu identifizieren. Sämtliche, hier aufgeführten Punkte werden in den folgenden Qualifizierungsschritten geprüft und abgearbeitet.
Designqualifizierung [DQ]: Liefert einen dokumentierten Nachweis, dass die Anforderungen aus den Nutzeranforderungen sowie gültiger Spezifikationen erstellt und gemäß den Good Practices berücksichtigt und umgesetzt wurden.
Installationsqualifizierung [IQ]: Bei diesem Qualifizierungsschritt wird überprüft, ob das Gerät oder die Anlage gemäß den Herstellerspezifikationen installiert wurde. Dies umfasst Aspekte wie die korrekte Platzierung des Geräts, die Verbindung zu Versorgungsleitungen, die Installation von Zubehör und die Dokumentation der Installationsschritte. Die Installationsqualifizierung stellt sicher, dass das Gerät oder die Anlage in einer kontrollierten Umgebung verwendet wird, die dessen ordnungsgemäßen Betrieb unterstützt.
Funktionsqualifizierung [OQ] Operational Qualification: Nach der ordnungsgemäßen Installation wird die Leistungsfähigkeit des Geräts oder der Anlage unter normalen Betriebsbedingungen überprüft. Dies umfasst typischerweise Tests zur Überprüfung der Genauigkeit, der Reproduzierbarkeit und der Leistung. Beispielsweise können Kalibrierungstests durchgeführt werden, um sicherzustellen, dass Geräte / Anlagen Messungen innerhalb akzeptabler Toleranzen durchführen. Die Funktionsqualifizierung stellt sicher, dass das Gerät seine Funktionen den Erwartungen entsprechend ausführen kann.
Leistungsqualifizierung [PQ] Performance Qualification: Im Zuge der Leistungsqualifizierung wird das Gerät daraufhin getestet, ob es konsistente Ergebnisse gemäß den spezifizierten Anforderungen liefert. Hierzu werden Tests aus der Routine simuliert, jedoch auch Belastungstests, um die Leistungsfähigkeit des Geräts unter extremen Bedingungen zu überprüfen. Die Leistungsqualifizierung ist entscheidend, um sicherzustellen, dass das Gerät in der Routine zuverlässig und reproduzierbar arbeitet.
Zu jedem Qualifizierungsschritt gehört zunächst ein Qualifizierungsplan, welcher vor der Durchführung geprüft und genehmigt werden muss. Die meisten Unternehmen haben hierfür standardisierte Prüfpunkte in ihren Arbeitsanweisungen und Templates definiert, welche durch systemspezifische Prüfpunkte ergänzt werden.Im Anschluss können die Prüfung vorgenommen werden, wobei entsprechend der guten Dokumentationspraxis vollständig, zeitnah und korrekt dokumentiert werden muss. Der Prozess wird mit einem Qualifizierungsbericht, der alle Ergebnisse und Mängelbetrachtungen enthält, abgeschlossen.
Betriebliche Nutzung und Überwachung: Nachdem der abschießende Qualifizierungsbericht von der Qualitätssicherung freigegeben wurde, kann das Gerät bzw. die Anlage in den regulären Betrieb überführt werden.
Es ist wichtig das Gerät bzw. die Anlage in der Routine kontinuierlich weiter zu überwachen, um sicher zu stellen, dass sein Zweck über die gesamte Lebensdauer ordnungsgemäß erfüllt wird. Geeignete Mittel hierfür sind die regelmäßige Kalibrierung von Messgeräten, die Überwachung von Betriebsparametern und die Schulung von Bedienpersonal. Außerdem werden Requalifizierungen geplant deren Häufigkeit risikobasiert festgelegt wird; üblicherweise spätestens alle 3 Jahre.
FAZIT
Gewissenhafte Durchführungen von Gerätequalifizierungen haben einen hohen Stellenwert für die Gewährleistung der Qualität und Zuverlässigkeit von Produkten und Prozessen in regulierten Branchen. Sorgfältig geplante und durchgeführte Qualifizierungsmaßnahmen stellen sicher, dass Geräte und Anlagen Qualitätsstandards und -ansprüchen entsprechen, regulatorische Anforderungen erfüllen und sich reproduzierbar und erwartungsgemäß verhalten.
Autorin: Maria Hissung